Werkstatt Teil 4Da nun alle Teile der Werkbank fertig verleimt, die Unterschränke ebenfalls fertig bestückt und bereit zur Montage waren, war es an der Zeit, alles mal zusammen zu stellen und auszurichten.
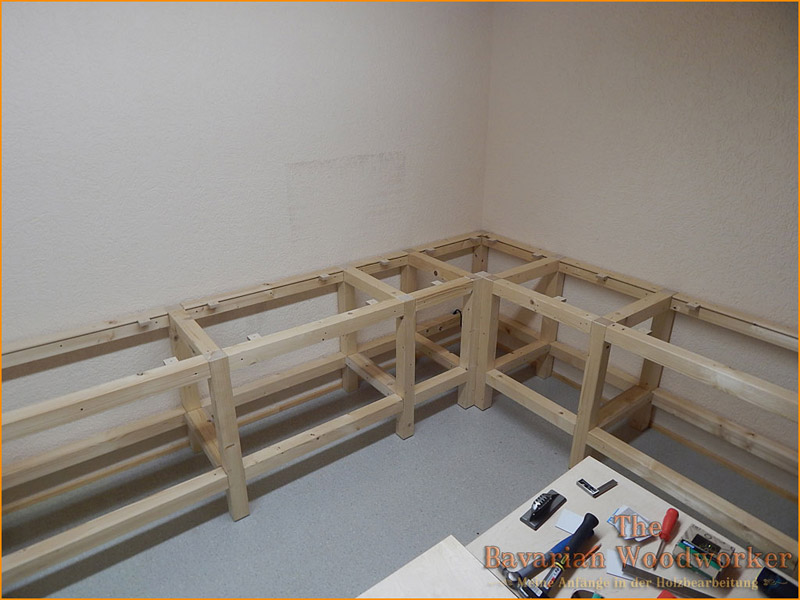
Der fertig montierte und ausgerichtete „Grundrahmen“ der Bank. Der Boden war schön gerade – zu sehen sind auch die bereits eingesteckten Nutklötzchen.
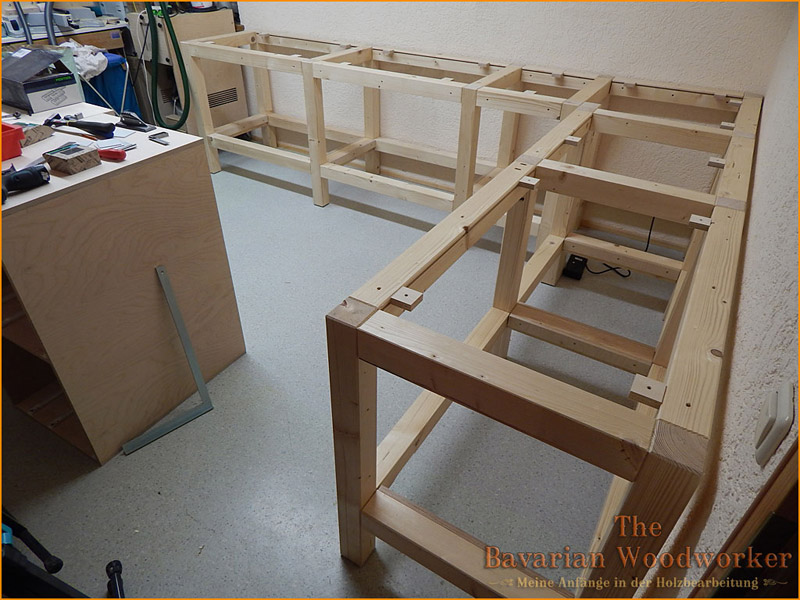
Nur die Wand war nicht so wirklich gerade, da musste ich ein wenig mit der Platte und der Abschlussleiste tricksen.
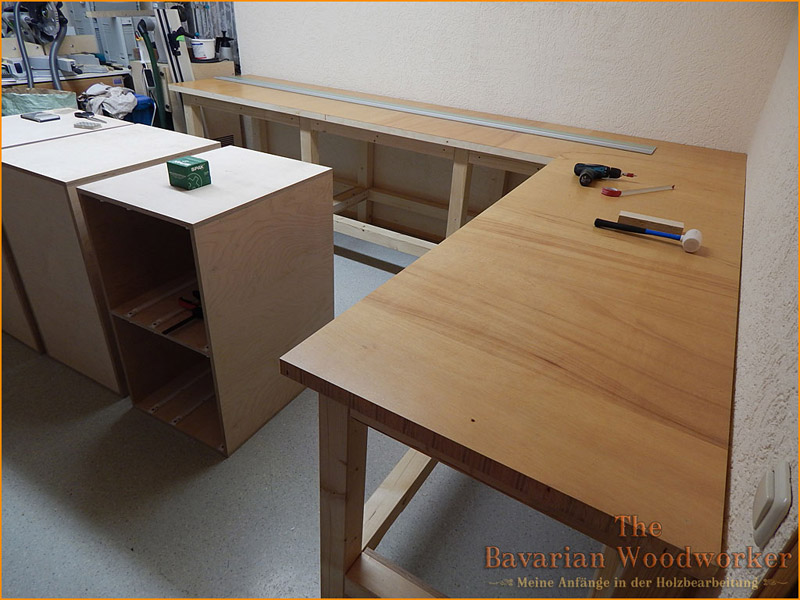
Nun aber endlich drauf mit den Platten und gleich festgeschraubt. Wieder zwei Teile, die aus dem Weg sind.
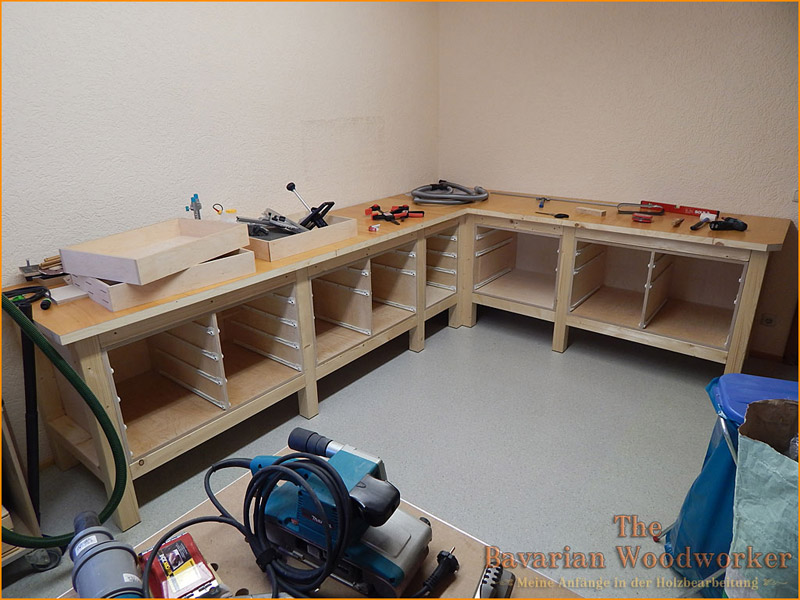
Dann noch die Unterschränke rein und es wird langsam Platz in der Bude.
Da ich ja meist allein in meiner Werkstatt werkle, die Unterschränke aber schon ein wenig schwerer waren wie ein Pfund Leberkäs, musste ich mir hier zwischendurch noch eine kleine „Hilfsrampe“ bauen. Leider hab ich davon kein Foto. Aber ohne das Teil hätt ich die Unterschränke nicht gerade und ohne verkanten reinschieben können. Zumal die wirklich „saugend“ reinpassten.
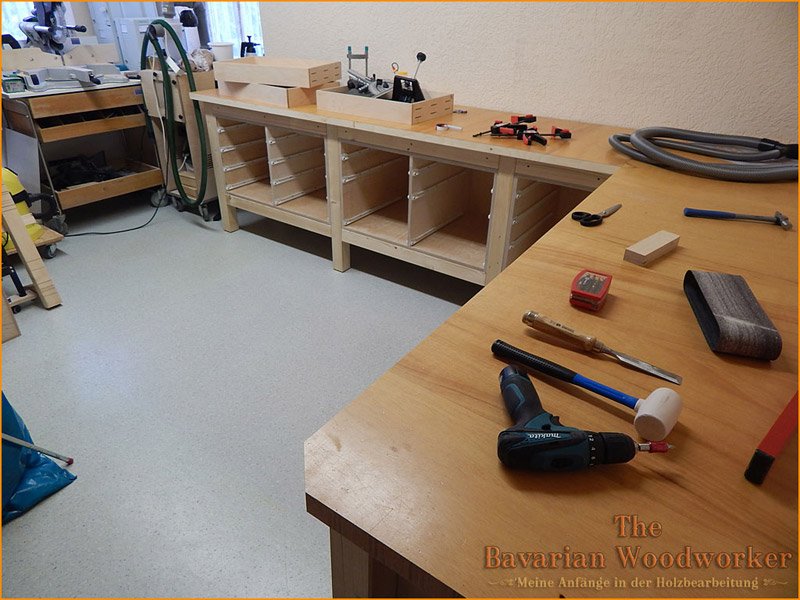
Nachdem ich mir dann das dritte Mal an dieser „blöden“ Ecke einen blauen Fleck geholt hab (natürlich immer an der gleichen Stelle), hab ich das der TS 55 überlassen, hier für mehr Arbeitssicherheit zu sorgen…:-)
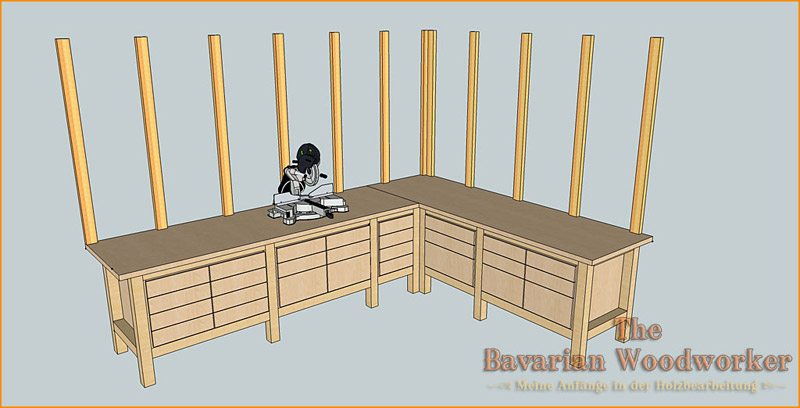
Wandverkleidung in der Planungsphase…
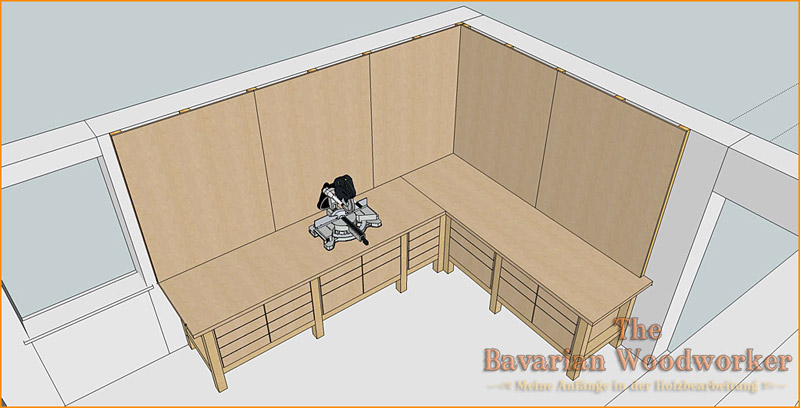
Verwendetes Plattenmaterial: Birke Multiplex in 15 mm.
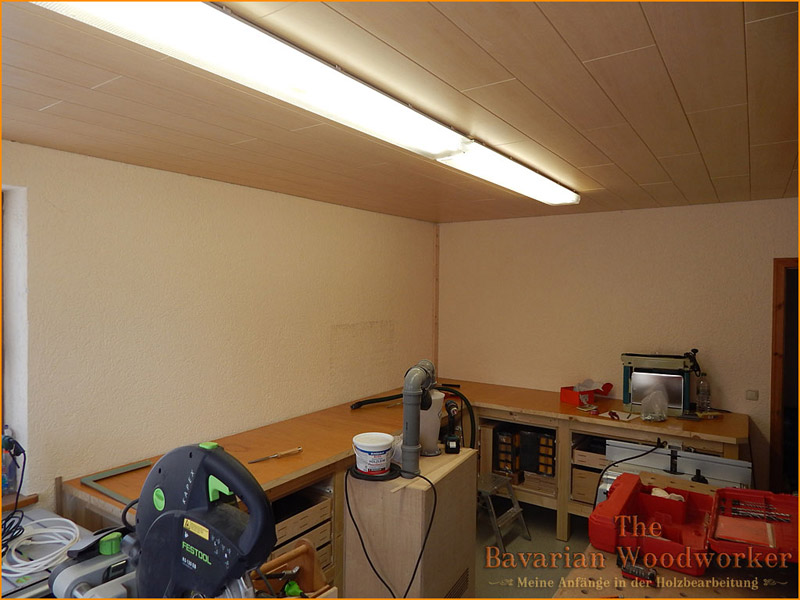
Wandverkleidung in Aktion….
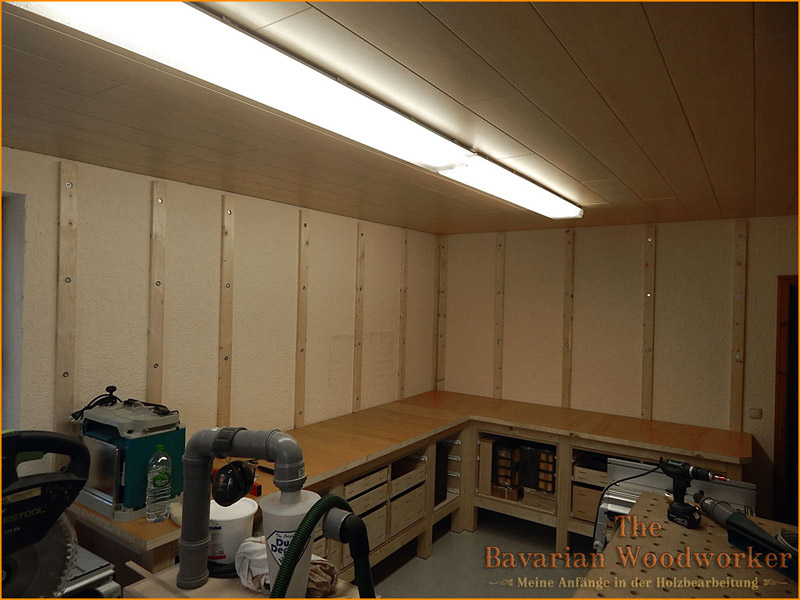
Die Lattung steht…
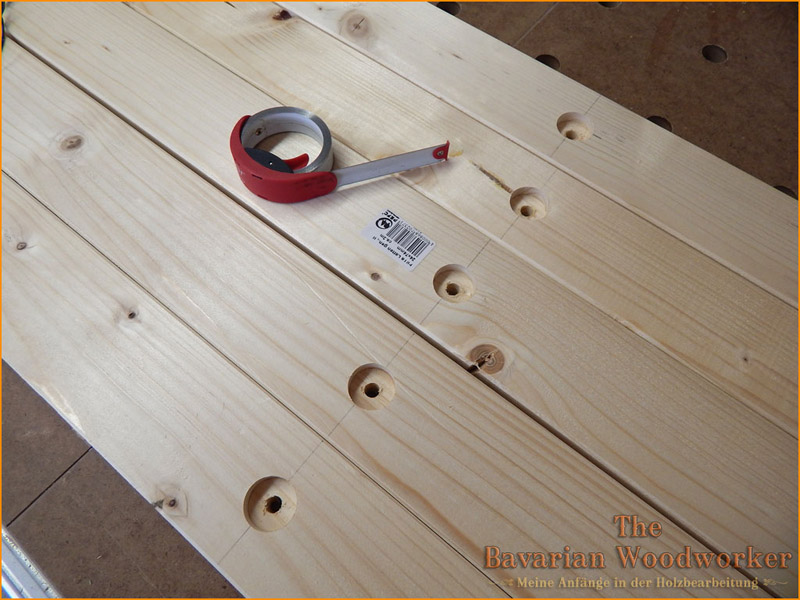
Unterkonstruktion Fichte 24 x 74 mm.
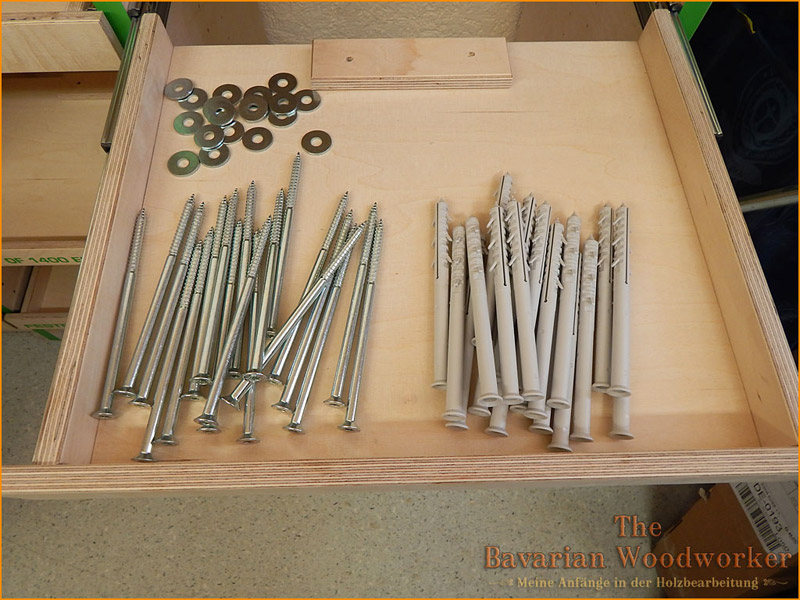
Torx-Schrauben 10 x 140 mm mit Hohlblockdübel sorgen für guten Halt der Lattung.
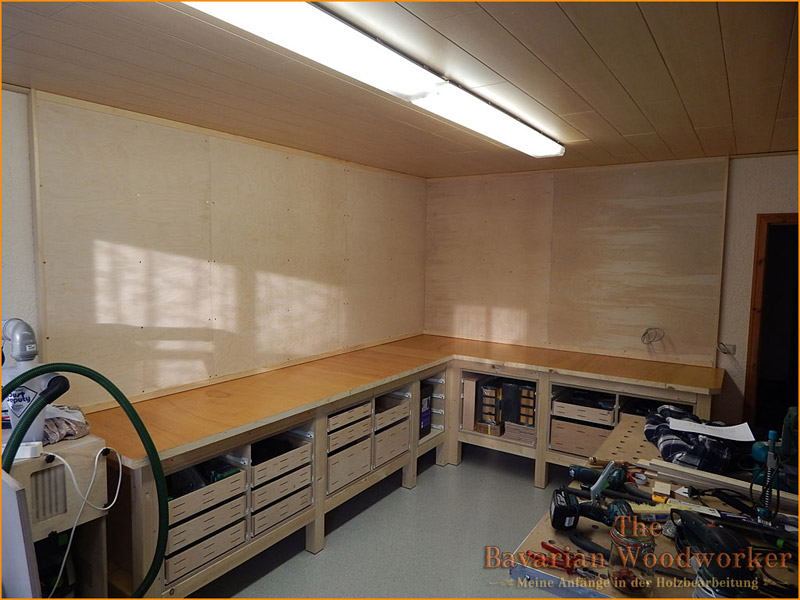
Platten drauf und noch die Abschlussleisten (Fichte) rumgetackert. In letzter Minute hab ich noch an das Kabel für den Kabelkanal gedacht…
Die Schubläden-Vorderstücke und die vordere Abschlussleiste für die Werkbank müssen warten, bis die „groben“ Arbeiten fertig sind. Da gibts sonst bestimmt noch die ein oder andere Delle. Jaaaa…ich weis – ist nur ne Werkstatt…:-)
Zu guter Letzt noch ein paar Gedanken, was meinen Tick für genaues Arbeiten angeht. Die zwei Stunden, die ich für den Bau der drei Vorrichtungen für die Domino XL „vertan“ hab, (ich wusste ja im Vorfeld auch nicht, ob das wirklich so funktionieren würde) haben sich voll ausgezahlt. Ich bin davon überzeugt, das, wenn ich die einzelnen Fräsungen für die Domino-Dübel nicht so pass- und wiederholgenau hinbekommen hätte, die Unterschränke am Ende nicht so super reingerutscht wären. Ich musste nur ein Kantholz ein wenig „nachputzen“, da dieses sich scheinbar ein wenig „gedreht“ hatte. War aber mit meinem kleinen Ralli-Handhobel schnell behoben.
Für mich ist es bei meinen Projekten nicht so ausschlaggebend, das ein Arbeitsablauf „so schnell wie möglich“ durchgezogen wird. Bei diesem wunderschönen Hobby ist doch der Weg zum Ziel bereits mehr als das halbe Vergnügen. Viel wichtiger ist mir dabei, meine Lernkurve stetig von Projekt zu Projekt zu steigern und dabei zu lernen, meine Hände und meinen Maschinenpark so effektiv wie es mir möglich ist, einzusetzen. Und auch, wenns nur Werkstattmöbel sind – wo kann man seine Skills besser pushen, sich besser mit seinen Maschinchen vertraut machen als bei solchen Projekten, wo man nicht gleich bei der Besten aller Ehefrauen Rede und Antwort stehen muss, wenn mal was nicht soooo gut geworden ist….

Was nun den von OlliT angesprochenen „zeitlichen Vorteil“ beim Bau solcher Vorrichtungen angeht, so muss ich sagen, das es evtl. mit reinem Anreißen schneller gegangen wäre. Aber – wäre es auch so genau geworden? Wieviele Meßfehler und Ungenauigkeiten hätten sich eingeschlichen und hätten mich durch deren Beseitigung wieder in der Zeit zurück geworfen?
Und um die Fragen von Olli und Klaus noch zu beantworten und weil sich für diese doch recht einfache Vorrichtung ein eigener Thread nicht lohnt, hier noch ein paar Bilder von meiner Domino-XL-Hilfskonstruktion zum Setzen der Fräsungen für die Domino-Dübel.
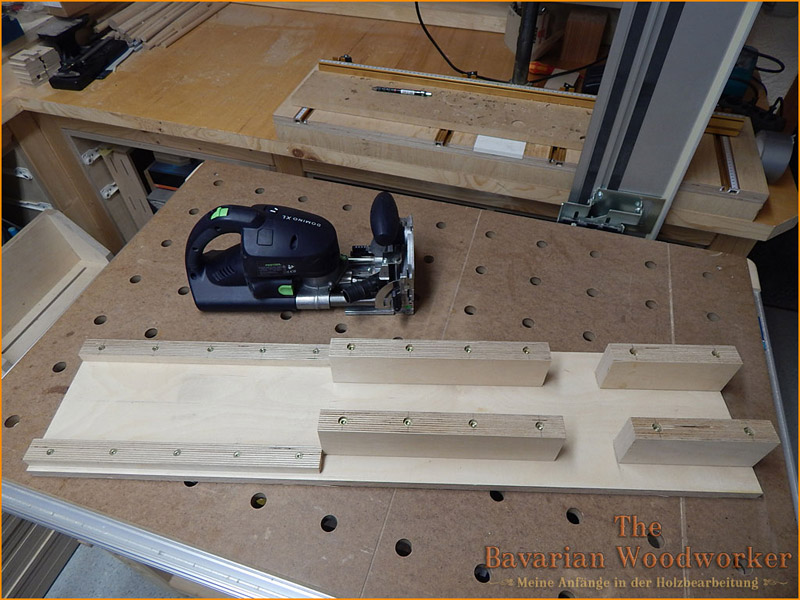
Hier die beiden Kontrahenden…Domino XL und Grundgestell der Vorrichtung. Verwendetes Material: Verschiedene Multiplex Reste in unterschiedlichen Stärken von 18 – 30 mm. Damit hinterher auch alles zu 100% passgenau wird, muss die Mittelachse der Domino-XL mit der Mittelachse der Werkstücke genau fluchten. Auch sollte der 90° Winkel genau passen. Was den Abstand der Schablonen zum Grundgestell angeht, so richtet sich der nach dem Abstand der Domino-Dübel zueinander. In meinem Fall waren es 50 mm von Mittelpunkt zu Mittelpunkt der 10 x 80 mm Domino-Dübel.
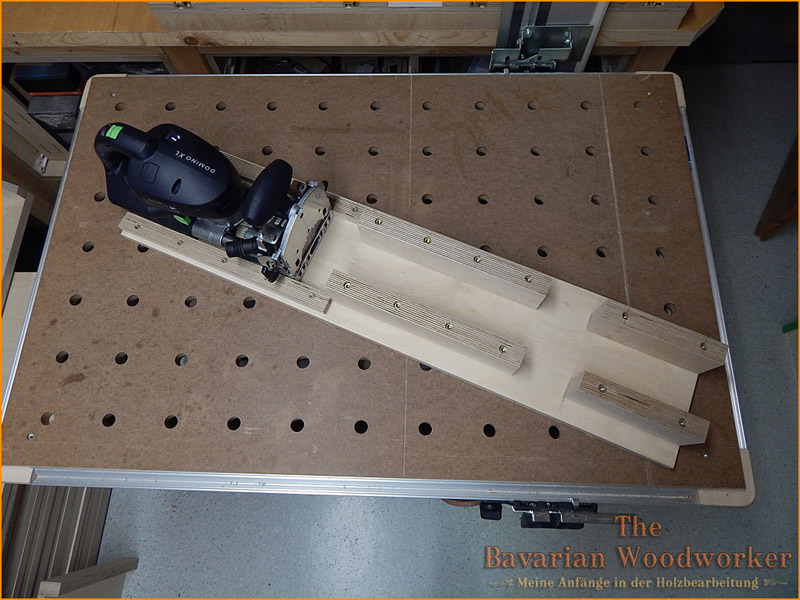
Hier kommt die Domino XL rein…
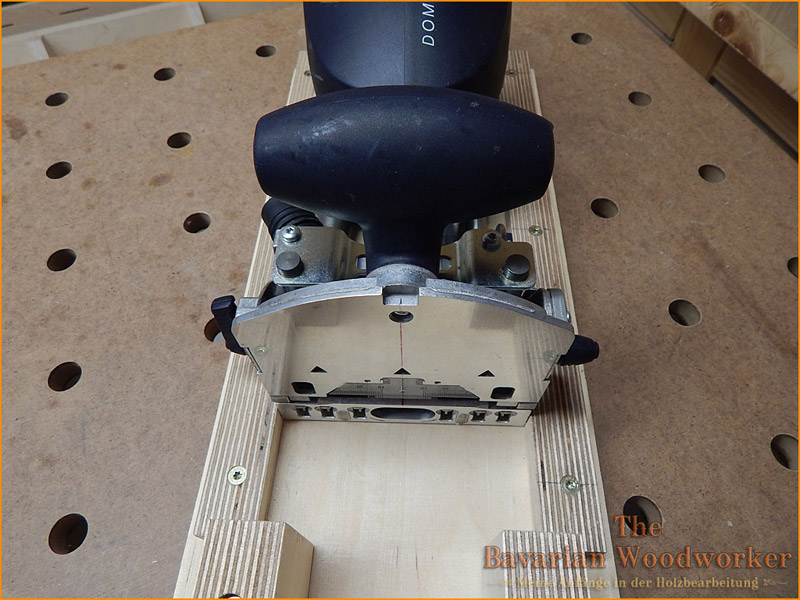
und gleitet passgenau in den Führungen….
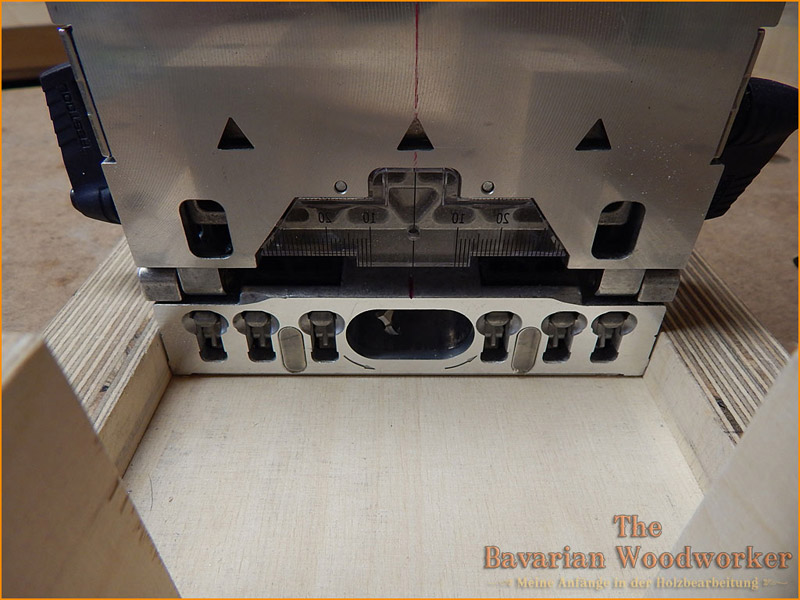
Absolut spielfreier Sitz. Hier sieht man auch recht gut die drei jeweils rechts und links des Fräsbohrers angeordneten Stifte, die, wenn ausgeklappt, manche Vorrichtung ersetzen. Leider konnte ich die bei diesem Projekt nicht nutzen, da es mit den unterschiedlichen Domino-Dübel Abständen und Anordnungen nicht geklappt hätte.
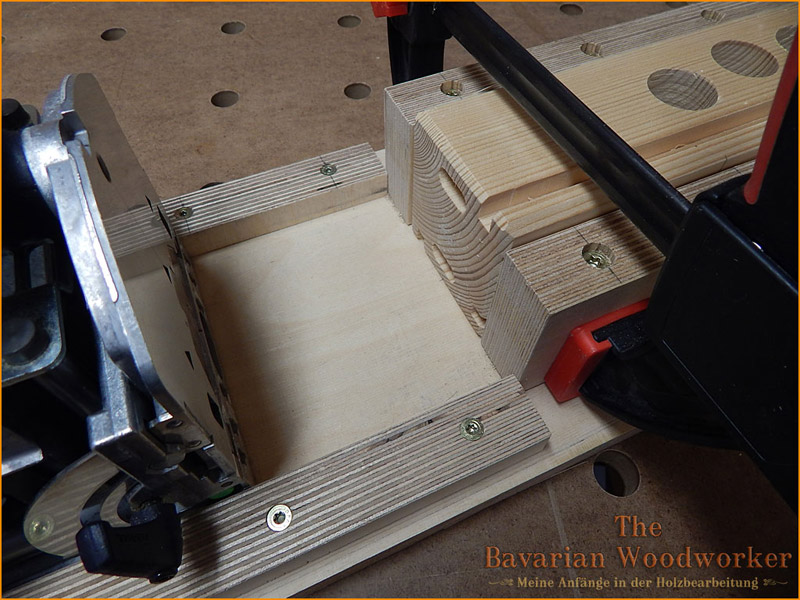
Auf der rechten Seite des Grundgestells wird das zu fräsende Werkstück eingelegt (leider hatte ich aktuell nur noch „verbohrte“ Reste der Kanthölzer, also bitte nicht wundern, wenn da schon Bohrungen usw. vorhanden sind) kurz mit der Einhandzwinge geklemmt – Fräse nach vorne schieben – fräsen. Schon ist die untere Fräsung erledigt.
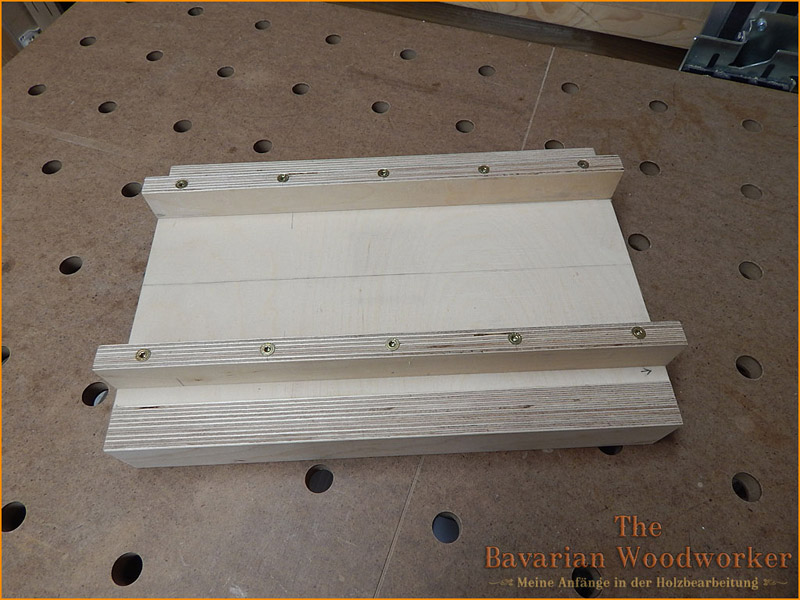
Um nun die obere Fräsung einzubringen, wird Teil 2 der Vorrichtung benötigt….
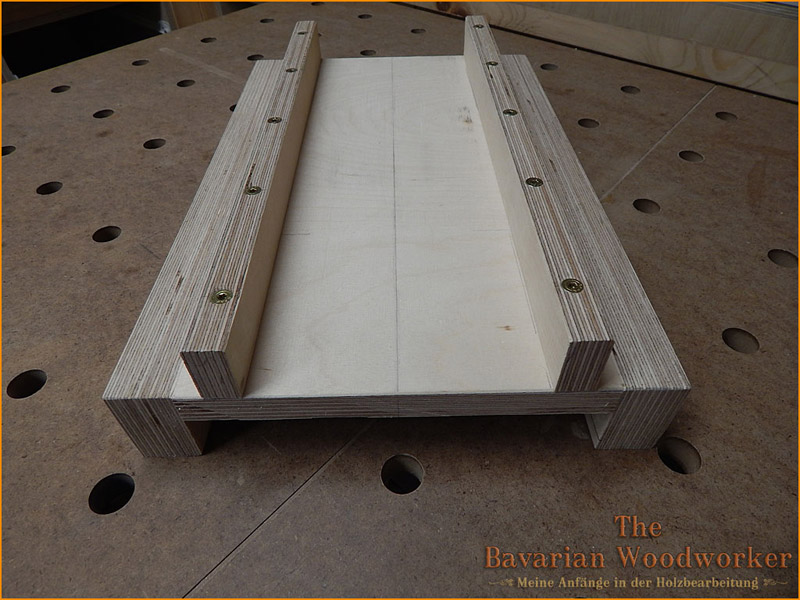
Teil 2 Vorderansicht – gebaut wie ein Schiebeschlitten. Die Höhe der hier verwendeten 30 mm Seitenwangen legt den späteren Abstand der Domino-Dübel fest.
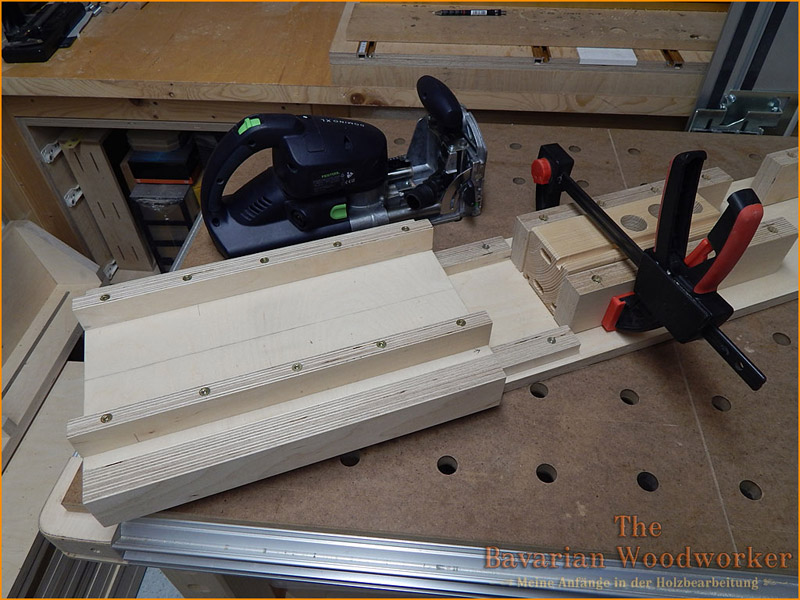
Teil 2 auf Grundgstell aufsetzen – passt saugend drauf. Auch hier ist es wichtig, das die Domino-XL wieder spielfrei in der Führung gleitet.
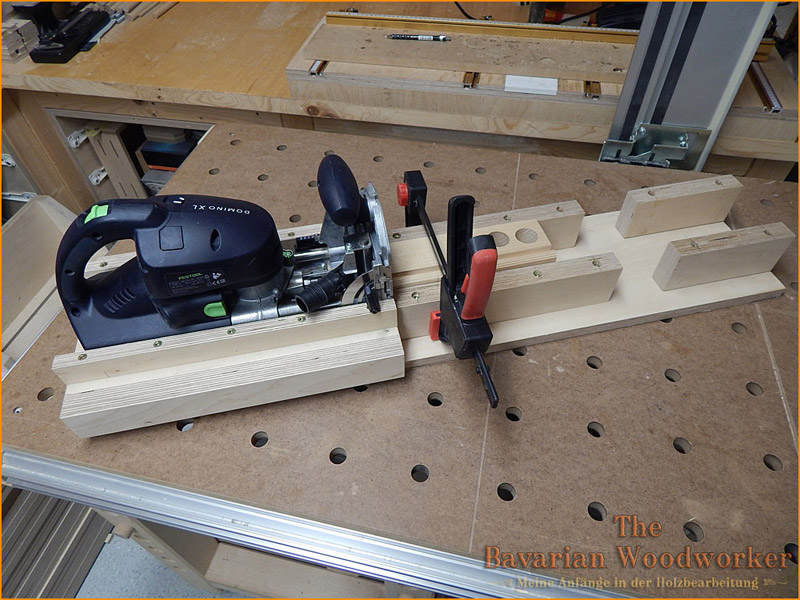
Fräse drauf – fräsen – fertig ist die obere Fräsung.
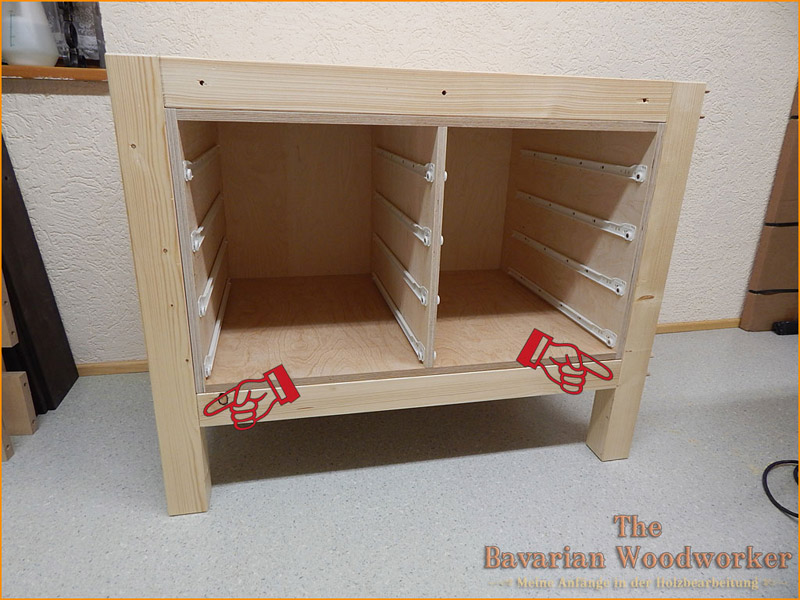
Um nun die Fräsungen für die Querhölzer einzubringen,
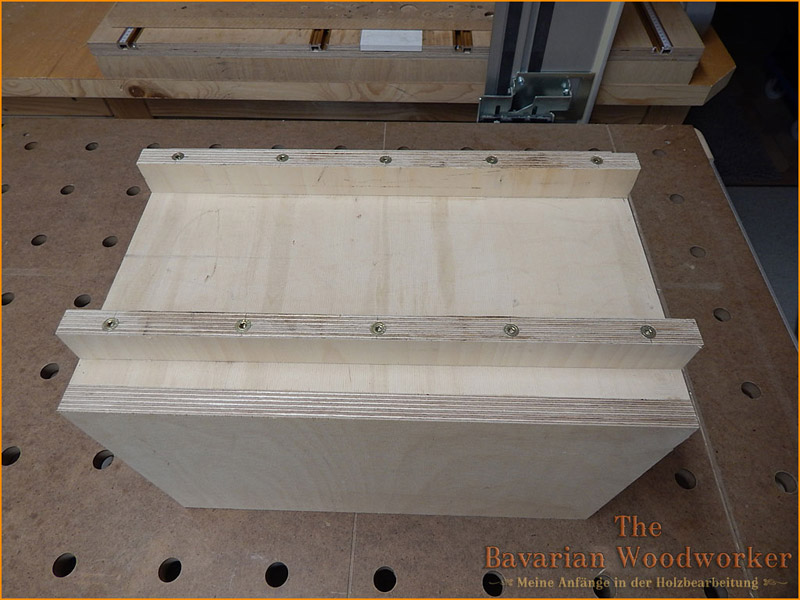
kommt Teil Nr. 3 der Vorrichtung zum Einsatz.
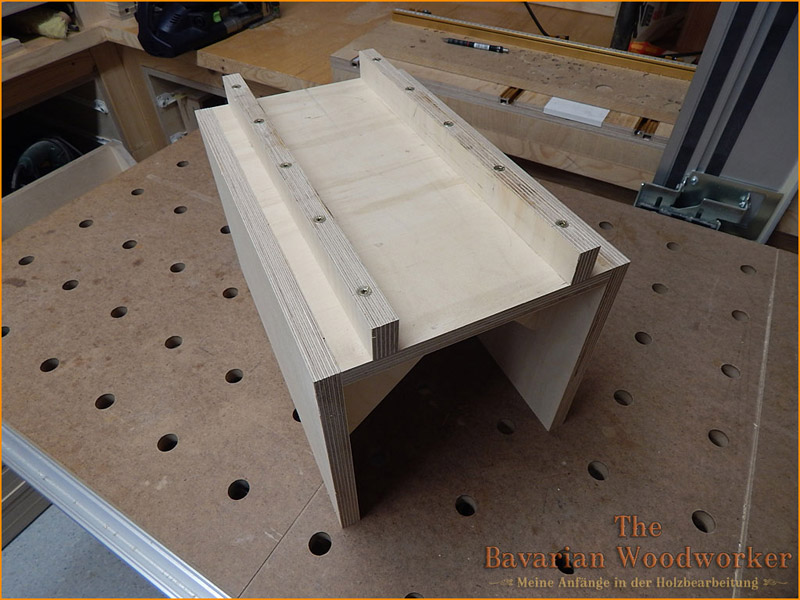
Hier in der Vorderansicht. Mit den Seitenwangen der Vorrichtung wird wieder die Höhe der unteren Fräsung festgelegt.
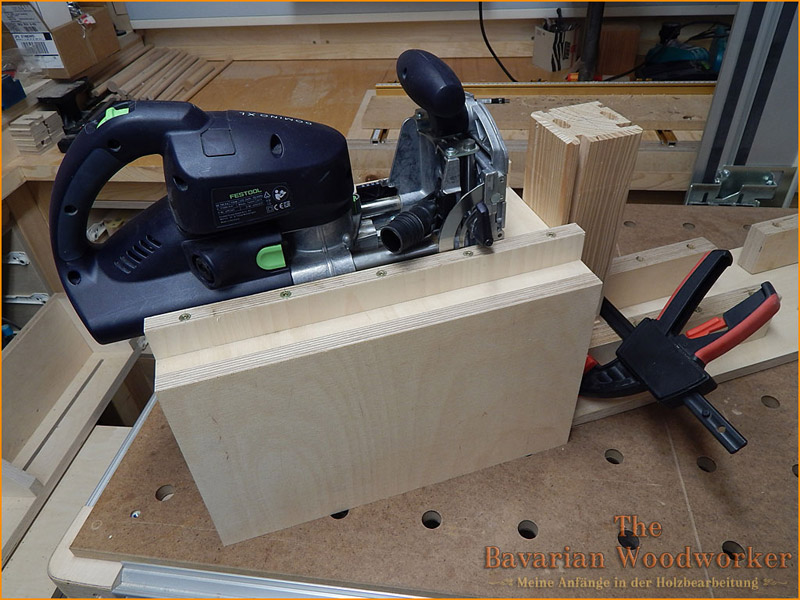
Teil 3 der Vorrichtung auf Grundgestell aufstecken, das Kantholz diesmal hochkant einspannen, festzwingen und losfräsen. Fertig ist die untere Fräsung.

Teil Nr. 2 auf Teil Nr. 3 aufstecken, um die obere Fräsung einzubringen.
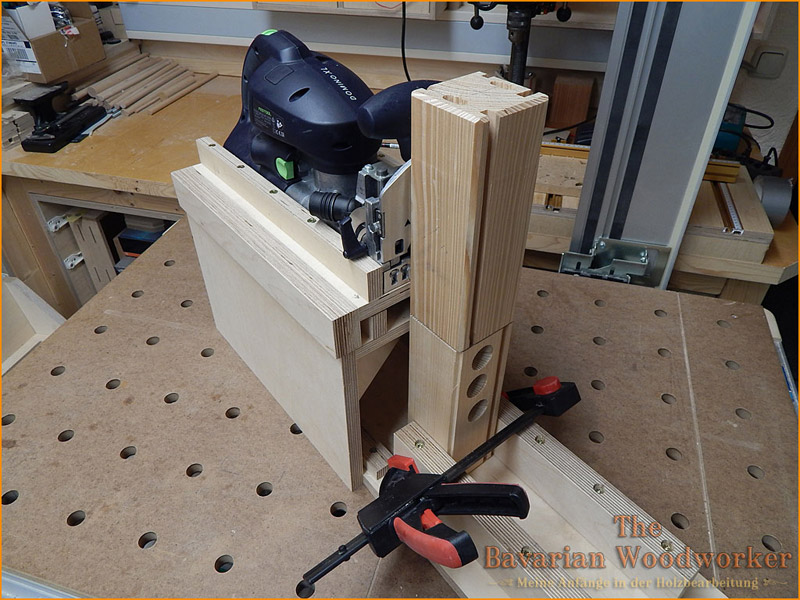
Teil Nr. 2 legt auch hier wieder den Abstand der Domino-Dübel fest. (Bitte nicht wundern wegen der „gestückelten“ Werkstücke. Leider hatte ich nur noch diese beiden Reststücke. Aber zur Demonstration sollte es reichen) Auf diese Art und Weise habe ich alle Dominos in die Werkbank eingebracht. Dauer ca. 1 Stunde für alle Fräsungen. Ein weiterer Grund, warum ich mir diese Vorrichtungen gebaut habe, ist, das ich sie auch noch für den MFT-Nachbau und den Frästisch brauchen werde, weil die von der Unterkonstuktion ähnlich sind. Hierzu folgen dann noch eigene Bauberichte.
Ich hoffe, ich konnte das einigermaßen verständlich erklären, sollte es noch Fragen dazu geben, dann immer her damit….

Servus, der Lothar